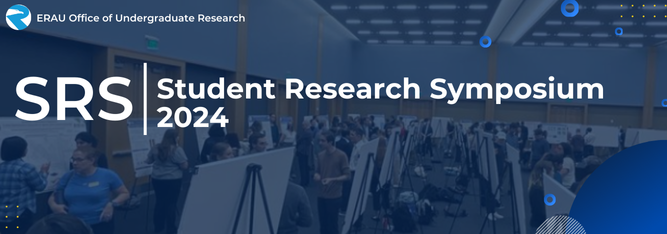
Cost-Effective Small Unit Composite Structure Manufacturing
Is this project an undergraduate, graduate, or faculty project?
Undergraduate
individual
Authors' Class Standing
Nihal Pradhan, Senior
Lead Presenter's Name
Nihal Pradhan
Faculty Mentor Name
Darris White
Abstract
The anticipated results of this research is an expanded understanding of composite structures and the analysis of multiple composite lay-up processes to determine the most efficient and cost-effective method for layup of larger and more complex components. Currently on campus there are few resources when it comes to complex lay-ups or development for composite structures, and knowledge of such procedures is spread through multiple departments and disciplines. This makes it very difficult for all teams to create their ideal components and forces them to create different designs utilizing more available methods at the expense of weight, performance and aesthetics. Some teams resort to out-of-house manufacturing, resulting in very expensive components that eats away at their project budgets and causes compromises in other areas of the end product. The main goal of this research is to determine the feasibility of manufacturing a carbon fibre monocoque for the Embry-Riddle FSAE team. However if the results prove that a monocoque can be manufactured, the research is expected to benefit all other teams in the university as it will provide a well documented method for other teams to manufacture their own complex composite components. The result of removing this obstacle could create an increase of performance and creativity across all teams as they are able to manufacture custom components such as airfoils with complex sweeps and chambers, or lighter and stiffer chassis for all vehicle teams, and even complex structures for robotic components on all the robotic teams.
Did this research project receive funding support from the Office of Undergraduate Research.
No
Cost-Effective Small Unit Composite Structure Manufacturing
The anticipated results of this research is an expanded understanding of composite structures and the analysis of multiple composite lay-up processes to determine the most efficient and cost-effective method for layup of larger and more complex components. Currently on campus there are few resources when it comes to complex lay-ups or development for composite structures, and knowledge of such procedures is spread through multiple departments and disciplines. This makes it very difficult for all teams to create their ideal components and forces them to create different designs utilizing more available methods at the expense of weight, performance and aesthetics. Some teams resort to out-of-house manufacturing, resulting in very expensive components that eats away at their project budgets and causes compromises in other areas of the end product. The main goal of this research is to determine the feasibility of manufacturing a carbon fibre monocoque for the Embry-Riddle FSAE team. However if the results prove that a monocoque can be manufactured, the research is expected to benefit all other teams in the university as it will provide a well documented method for other teams to manufacture their own complex composite components. The result of removing this obstacle could create an increase of performance and creativity across all teams as they are able to manufacture custom components such as airfoils with complex sweeps and chambers, or lighter and stiffer chassis for all vehicle teams, and even complex structures for robotic components on all the robotic teams.